June 9, 2021
Lean Into the New Normal: Lean-Agile Management for What’s Next (Part 1)
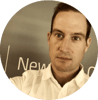
Written by: Christopher Pola
This post is part one of a two-part series. Lean-Agile Management principles can help you lean into the “new normal” and prepare for what’s next. Read on to learn about the causes of waste and why it’s important to eliminate it.
I think it is fair to say that there is a lot of humbug around the phrase “new normal” or “next normal”. These phrases refer to how quickly a company can adapt its operating model for success, and you must apply lean-agile management practices to bolster your organizational capacity to do just that.
Lean-agile management will allow your organization to be resilient by freeing up the latent capacity essential to managing change. Your organization will be prepared to take on the “new normal” without the need for additional investment. In this blog post, I focus on the lean principle of Eliminating Waste and provide tangible examples of lean practices that eliminate non-value-add transactions across the enterprise.
Why Eliminating Waste is of Vital Importance
First things first, why is eliminating waste a topic of vital importance? It isn’t uncommon to see a lot of work duplication and redundant processes inside organizations.
A lean enterprise will recognize that waste and eliminate it because people’s time and cognitive capacity are finite. If people don’t have the capacity or space to respond to change creatively, then improvement comes at a snail’s pace or not at all.
People are the heart of your organization. The advantages to eliminating waste in your processes and freeing up time from non-value-add activities are exponential. Just think about the benefits of the 15% rule at 3M or 20% project at Google; do you even have the capacity for holding hackathons?
Another form of waste that I commonly observe is what I dub the ‘busyness syndrome’ – a hive of people creating and managing 3x times the amount of work an organization can realistically complete at that moment in time. Immediately we recognize that this situation violates other lean-agile principles like Limiting WIP (Work In Progress).
If left unchecked, working like this eventually ushers in complications attributed to Queueing Theory. If you are already loading too much work into the system, then the number of transactions has increased exponentially: a double whammy against those transformation goals. Understanding capacity and limiting work to capacity is something a lean-agile solution will help you master.
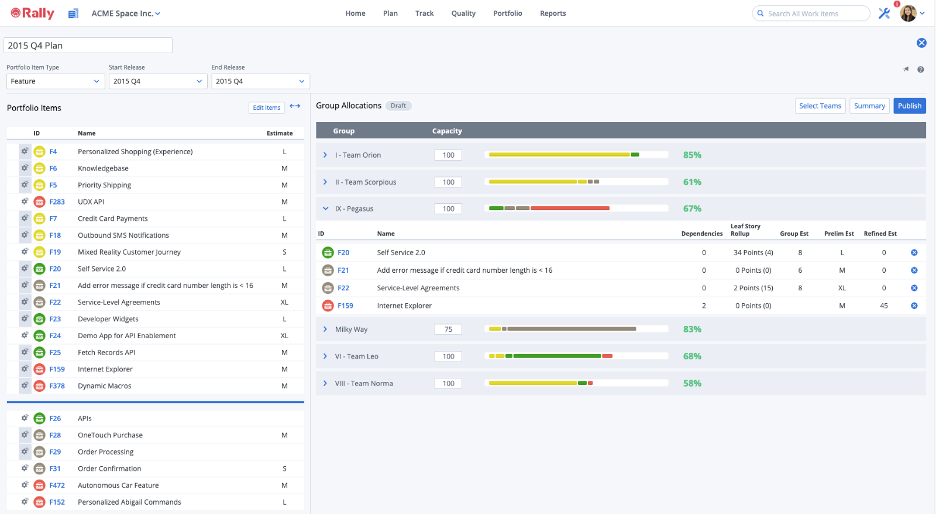
A fundamental theme in the lean-agile paradigm is that all transactions are some form of waste. Repeat that to yourself ten times.
As a leader, if you purposefully eliminate the unnecessary non-value-add transactions, you have a better chance at yielding operational improvements. Understand that there are necessary non-value-add transactions too, but that’s not the focus here. It’s the non-value-add internal controls, processes, and proxy transactions we create to manage everything that needs to be examined and eliminated.
What Causes Waste
Have you ever stopped to think about how all this busy work comes into being? It’s not by luck. Generally, it occurs when there is a lack of significant controls inherent within your processes and systems and an absence of lean-agile thinking.
Detailed transaction-based tracking becomes the proxy for financial and operational control. Silos of people, processes, data, and technology can be the cause. Unfit-for-purpose technology is also a big culprit.
The effect is that business, portfolio, program, and delivery team stakeholders manage work in separate systems. Spreadsheets are used as a stop-gap to manage these unconnected backlogs. A cascade of essential conversations, decisions, and compliance activities are all now keyed off these proxy transactions in a spreadsheet.
If you are thinking, “How does that even lead to good decision-making?” And hopefully, after reading this blog, that’s your “old normal”. The transactions in a spreadsheet, the email status report, the busywork to consolidate information from disparate and unstructured systems are all significant forms of waste.
The Importance of Having a Data Strategy
Most, if not all, transformations or new improvement initiatives overlook the importance of a data strategy. A data strategy goes hand-in-hand with technology solutions that will truly enable a transformed operating model end-to-end. The technology solution must allow people to perform the new practices, which lead to new behaviors and cultural change.
The big, bold idea here is that real operational control is reflected in the actual work that people and teams perform, and that should be captured natively in the systems they use. Portfolio management software should enable the end-to-end business process and reduce or eliminate the need to use proxy data or duplicate transactions in external systems for operational or financial governance.
The output of a team's regular work activities helps track costs and status. This shouldn’t stop at the system of record for product development. The principle of eliminating waste goes beyond your internal operations. With a systems-first approach, you can start to identify ways to improve transactions across the macro value stream view too.
It is just as crucial to improve processes and reduce the number of unnecessary non-value-add transactions required between your suppliers and customers. You must create or opt for lean partnerships to enhance transaction effectiveness and lower costs.
Don’t construe eliminating transactions as downsizing or furloughing employees. Eliminating waste as it applies to lean is anything but a shortsighted or short-term activity. It’s about building the controls into the company's internal operations and systems of record vs. overlaying additional processes and controls, such as manual tasks using proxy data.
Look for Part Two of this series coming soon. We will illustrate five examples of waste and how to eliminate them.
Visit Broadcom Enterprise Software Academy to learn more about how ValueOps and Rally Software can help you start your journey with lean-agile principles today.
Tag(s):
ValueOps
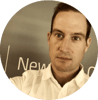
Christopher Pola
Christopher Pola is an Executive Advisor at Rally Software® - Agile Management segment of Broadcom Enterprise Software. In that role, he helps customers launch agile programs, proving the benefits of modern ways of working. Melding theory with a ‘hands-on’ plan-drive approach, he is experienced in all three facets of...
Other Resources You might be interested In
What’s Hiding in Your Wiring Closets?
See why you must move from periodic audits to a state of perpetual awareness. Track every change, validate it against policy, and understand its impact.
All Network Monitoring Tools Are Created Equal, Right?
See how observability platforms provide a unified view across multi-vendor environments and correlate network configuration changes with performance issues.
Scale Observability, Streamline Operations with AppNeta Monitoring Policies
This post reveals how, with AppNeta’s monitoring policies, you can leverage a powerful framework for scalable, flexible, and accurate network observability.
AppNeta: Current Network Violation Map Dashboard
Learn how to configure and use the Current Network Violation Map dashboard in AppNeta to identify geographic regions impacted by WAN performance issues.
AppNeta On-Prem: Minimize Unplanned Downtime
Learn how to configure the AppNeta On-Prem environment following best practices for high availability and disaster recovery to maintain service continuity and minimize unplanned downtime.
Rally Office Hours: August 7, 2025
Get tips on how to use the Capacity Planning feature in Rally, then follow the weekly Q&A session with Rally product experts.
dSeries Version 25.0 Boosts Insights, Security, and Operational Efficiency
Discover how ESP dSeries Workload Automation 25.0 represents a significant leap forward, making workload automation more secure, visible, and efficient.
What Your SD-WAN Isn't Telling You
SD-WAN's limited view blinds it to underlay issues. Augment SD-WAN with end-to-end visibility to validate decisions and diagnose root causes for network resilience.
How DX NetOps Topology Streamlines and Optimizes Triage
DX NetOps Topology gives you the context and clarity to stay ahead of problems and keep your networks running smoothly. Troubleshoot quickly and seamlessly.